 |
Préparation carbone !
Cette préparation a été effectuée par Denis COLLE
(alias Tartempion/Tartemuche).mai 2003 |
 |
Présentation
Comme
je l'ai dit dans un autre article sur Kweb, je suis passionné
de bricolage dans
tous les sens du terme et le modélisme TT permet en partie d'assouvir cette
passion.
Mon fils étant le pilote et moi le mécano.
Nous
avons débuté avec un MP6 sport qui à la longue n'était plus
tellement sport car j'ai
fait beaucoup d'améliorations dessus.
Ensuite, en septembre 2002, nous avons fait l'acquisition du
MP7.5 KANAI II.

La voiture : Visible en détail rubrique
Champion de Kweb
Ayant
trouvé à acheter des plaques de carbone à un prix très compétitif,
j'ai décidé de me lancer dans la réalisation d'un maximum de
pièces carbones pour ces deux voitures.
Je
vais, par cet article, vous présenter ma manière de procéder.
Je ne prétends pas détenir la bonne solution mais en tout
cas elle permet à moindre coût d'obtenir des pièces dont la
qualité et le rendu esthétique (ça compte aussi) sont tout à
fait corrects. A vous de voir ...
La matière première
Les plaques de carbone en ma
possession sont un peu particulières. C'est du carbone dit technique,
relativement brut, c'est à dire qui n'a pas le rendu totalement lisse et
brillant des pièces achetées dans le commerce. En conséquence, il faut, mais ça
dépend des goûts, le vernir après usinage pour s'approcher du rendu
professionnel. Ces plaques sont réalisées
en plusieurs plis de carbone croisées (environ 3 plis par mm d'épaisseur) et
pressées à
chaud en étuve à environ 150° (c'est du carbone de chez carbone !).
J'ai reçu les plaques brutes et je les
ai vernies après usinage. Les plaques font environ
38 x 16 cm pour 26 Euros. Je les ai achetées en 2.2, 3.5 et 4 mm d'épaisseur.
Avec ces surfaces et ces épaisseurs, il y a de quoi faire plusieurs voitures !
Pour présenter ma méthode et
faire des photos, j'ai refait le support AR du MP 7,5.
C'est en effet une pièce intéressante pour la démonstration visée. Par
contre, la plaque
de carbone utilisée avait été vernie avant usinage avec un restant de
vernis. |
 |
La
plaque en épaisseur 3,5 mm. |
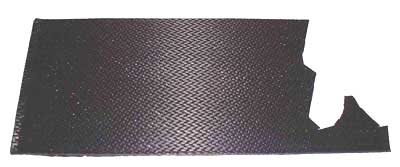 |
La
plaque en épaisseur 2,2 mm. |
Les outils nécessaires |
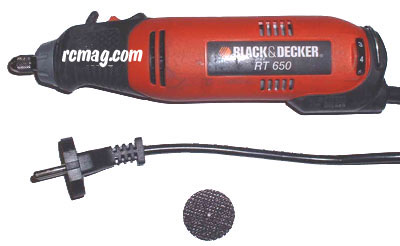 |
La mini perceuse
En
fait, c'est une mini perceuse de marque Black et Decker
directement branchée sur secteur 220 V et avec vitesse variable
(de 8000 à 27000 t/min ) qui est parfaite pour ce genre de
travail car elle dispose dun fort couple. Il faut utiliser le disque
de type armé de fibre de verre renforcée car il est incassable
et ne s'use pratiquement pas. C'est vraiment le disque à posséder
dès qu'il s'agit de découper des matériaux non métalliques
!
|
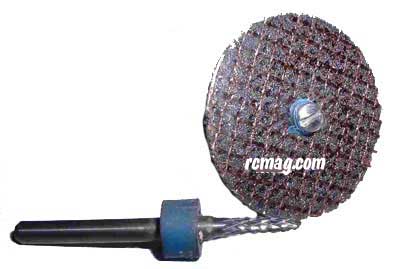 |
Pour "manger" la
matière pour faire les lumières dans les pièces, j'ai utilisé
une fraise carbone.
Pour ceux qui ont la "chance"
d'aller voir le dentiste, demandez lui les fraises qui sont usées
(pour lui). Pour vous, elles peuvent encore faire un petit peu de
bruit mais cette fois pour votre plaisir. Il en existe de différentes
formes et sont hyper solides. Continuez quand même à vous laver
les dents. Rassurez-vous la mienne ne vient pas de mon dentiste.
|
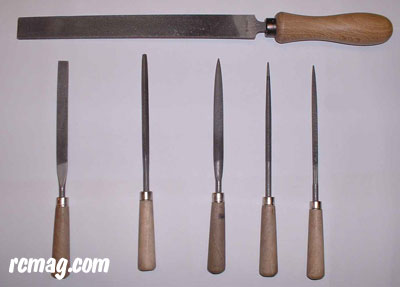 |
Les limes
Un assortiment de limes de
différentes tailles et formes pour s'adapter à tous les
contours des pièces. Prendre de préférence des limes à
denture fine pour un bon état de surface.
Lime plate, triangulaire,
ronde, carrée et demi-ronde. J'ai acheté un lot dans un magasin
de bricolage. Ce n'est pas du premier choix (vu le prix) mais
pour ce qui est à faire, ça va très bien.
|
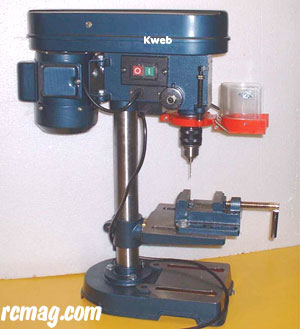 |
La grosse perceuse
Une perceuse de type
sensitive : Cela permet de faire des trous parfaitement
perpendiculaires à la plaque. Il s'agit bien de faire des pièces
de qualité comme les pros et pas de l'à peu près ! En fait
j'ai fait l'acquisition récente d'une perceuse à colonne (dans
le même magasin de bricolage que les limes) pour la somme
d'environ 60 Euros. Là encore, ce n'est pas du matériel pro
mais pour le non pro c'est amplement suffisant. Je m'en suis
servi pour faire la pièce des différentes photos à titre
d'exemple. Il faut bien entendu utiliser des forêts neufs ou
bien affûtés.
|
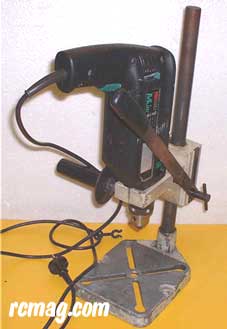 |
Toutes les pièces des deux
voitures MP6 et MP7,5 ont été faites avec une perceuse plus
simple mais aussi tout à fait adaptée. |
Venons en à La méthode
Phase 1
|
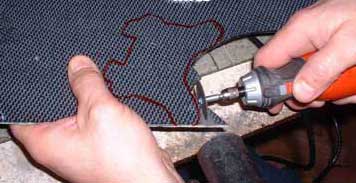 |
Le découpage grossier
(temps 2 min environ)
Tout d'abord, il faut découper
grossièrement la plaque (choisie de la bonne épaisseur) au
contour de la pièce en laissant au minimum environ 5 mm de marge.
Pour ce faire j'ai utilisé un feutre pour contourner la pièce
d'origine. Avec la disqueuse, on pratique par coupe en lignes
droites successives. La découpe du carbone avec cet outil, c'est
comme couper le beurre et je ne mens pas. En même temps, il faut
une personne qui aspire la poussière avec un aspirateur. |
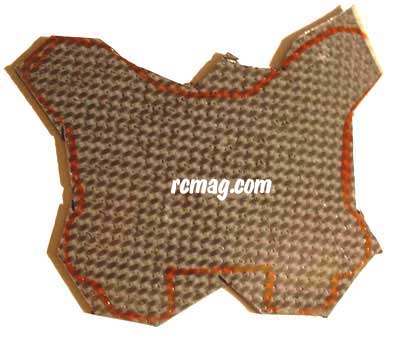 |
Ainsi, on arrive à grosso
modo ce type de découpe. Moi, je tiens le carbone et la
disqueuse à la main en prenant appui sur un établi. A vous de
voir la meilleure méthode à prendre. Le fait de tenir la pièce
à la main offre de la souplesse (amortissement) en cas de
coincement du disque.
Bon, on ne peut pas encore
le placer sur la voiture mais patience ...
 |
Phase 2 |
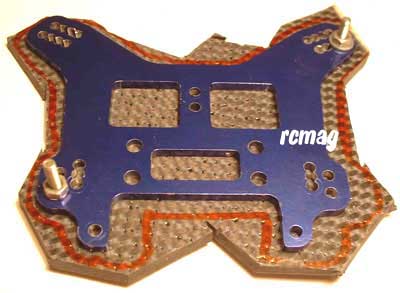 |
Le perçage
(temps
5 min environ)
Ensuite, vient l'étape du
perçage avec la perceuse sensitive. Généralement toutes les pièces
comportent plusieurs trous. J'utilise la pièce d'origine comme
guide de perçage. Tout d'abord, je perce un des trous (du bon
diamètre) sur une partie la plus périphérique possible (par
exemple une des oreilles sur un support d'amortisseur). La plaque
de carbone est alors tenue à la main ou avec une pince étau ou
... Ce trou étant fait, je serre fortement les deux plaques (carbone
et original) avec un boulon du diamètre adéquat en interposant
des rondelles pour ne pas "blesser" les pièces.
|
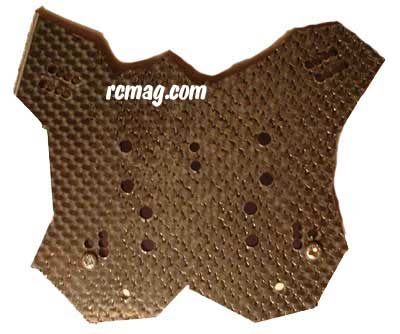 |
Ensuite, il suffit de faire
un deuxième trou (toujours du bon diamètre) le plus éloigné
du précédent (mais quand même sur les plaques). Ainsi en éloignant
les trous, on diminue les erreurs de positionnement. Là encore,
je fixe fortement les deux plaques. Ensuite vous avez en main
deux plaques intimement solidaires. Il reste ensuite à percer
tous les autres trous. Avec cette méthode, je suis même arrivé
à faire les trous des supports d'amortisseurs que se chevauchent
(2 rangée de 4 trous sur chaque oreille !).
Pour réaliser les évidements,
je perce des trous aux quatre coins et commence à "manger"
la matière au centre. |
Phase 3 |
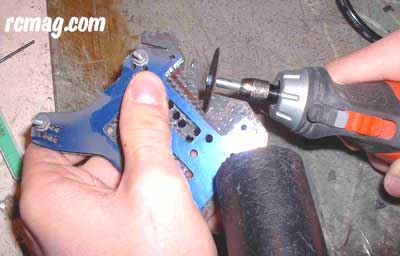 |
Le
meulage grossier
(temps 5 min environ)
Pour cette opération,
j'utilise la mini disqueuse toujours avec le même disque époxy.
Je tiens le couple de pièces (carbone + original vissés) d'une
main avec l'autre main la disqueuse et je contourne la pièce en enlevant le plus
possible de carbone mais en en laissant un tout petit peu.
|
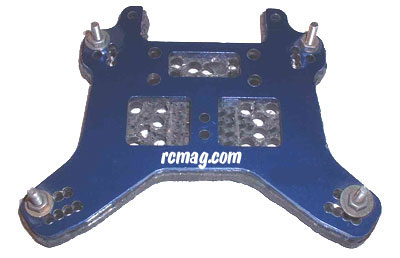 |
On arrive ainsi proche de la
pièce définitive
à environ 2 mm près.
Avec cette méthode, il y a beaucoup de poussière qui s'envole.
Ouf, il y a l'aspirateur ! |
Phase 4 |
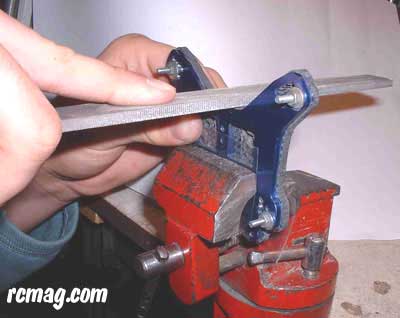 |
Le
meulage fin
(temps 30 min à 1 H environ)
Nous arrivons à la phase de
finition. Elle s'effectue à la main avec les limes du profil adéquat.
Le couple de pièces est fixé dans un étau en interposant une
couche de protection pour ne pas les abîmer (par exemple du
carton ou du plastique). Là, il faut y aller doucement en
restant toujours perpendiculaire à la pièce pour faire un bord
franc et ne pas abîmer la pièce originale ou du moins le moins
possible. Même le limage n'est pas anodin car on a vite fait
d'avoir un mouvement en forme de bascule, ce qu'il ne faut pas.
|
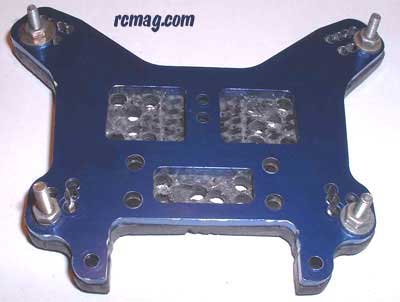 |
Dans certaine partie, il est
possible de laisser 0,5 mm de marge voire plus par rapport à l'original à
partir du moment où cela ne gênera pas le montage. C'est le cas du
pourtour des oreilles du support. Par contre, pour la partie inférieure
qui enjambe la cellule, il faut être pile poil ! |
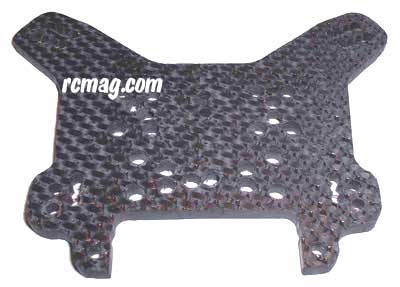 |
En y allant doucement on arrive
sans problème à ce résultat. |
Phase 5 |
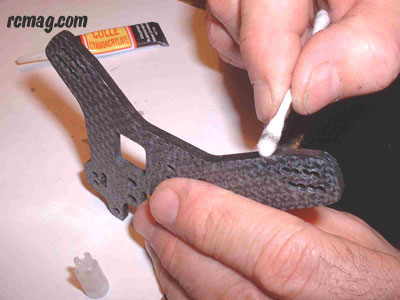 |
La
protection des pièces
(temps 2 min environ)
La plaque de carbone est
constituée de plusieurs couches de carbone croisées. Après
l'usinage, les bords sont relativement poreux et risquent de s'écailler,
de se délamelliser, voire de blesser le bricoleur par des échardes.
En conséquence, je dépose une fine couche de colle
cyanoacrylate liquide. Elle s'insinue en profondeur et colle
l'ensemble. Bien entendu prendre les précautions d'usage pour
l'utilisation de la cyano. Ne pas oublier de faire aussi les
trous. J'utilise un coton tige pour le pourtour et un cure dent
pour les trous. Ensuite, il n'y a plus de problème pour tripoter
les pièces. |
Phase 6 |
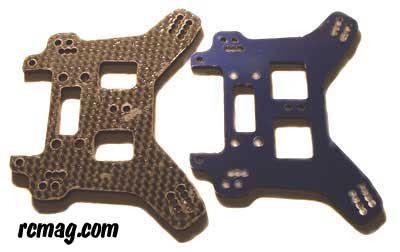 |
La
finition
Ca y est, la pièce est
totalement terminée. A comparer avec la pièce d'origine. Au jeu
des erreurs, vous remarquerez que la partie centrale est plus
large en carbone qu'en alu. J'ai estimé que cela donnerait plus
de rigidité.
|
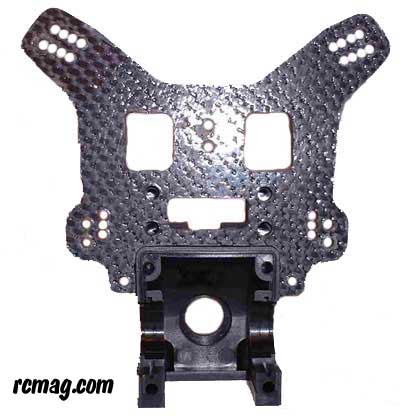 |
Comme je l'ai dit au début de
l'article, j'ai verni les pièces pour leur donner un certain look. Après
avoir utilisé du vitrificateur, du vernis normal, du vernis auto en bombe,
j'ai finalement opté pour du vernis à doubles composantes (vernis +
durcisseur) qui résiste un peu mieux au carburant ! ! . Je l'ai acheté à
un carrossier en petite quantité car il ne se trouve pas dans les magasins
courant mais uniquement pour les pros et donc en grosse quantité. |
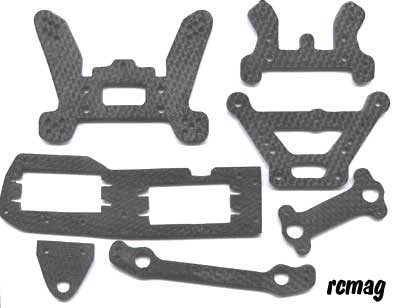 |
Voici toutes les pièces que
j'ai réalisées
pour le MP 6. Tout est en carbone sauf les
bavettes et les renforts AV et AR. |
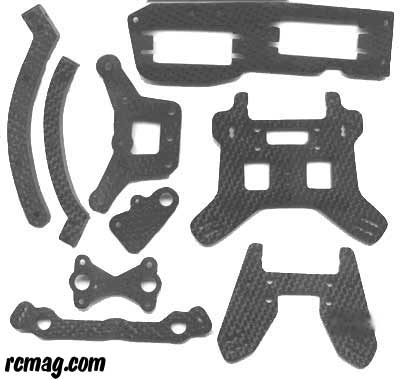 |
Voici toutes les pièces que j'ai
réalisées
pour le MP 7,5.
Tout est en carbone sauf les
bavettes. |
Gain de poids
Pour les pièces hors
renforts : gain de poids de 50 g sur les 82 g d'origine.
Pour les renforts pas de
gain mais super rigidité. Je pense que je pourrais encore alléger
mais je ne préfère pas trop aller aux limites.
Sur le MP6, nous avons roulé
toute la saison (course de ligue 1, masters, et championnat
espoir). Pas de problème ; absolument pas de casse.
Sur le MP7, nous n'avons
fait que la dernière course de ligue (le fiston a terminé 2éme
en espoir) et quelques entraînements vite arrêtés avec
l'automne. Nous avons eu un pliage du renfort AV que j'avais fait
initialement en épaisseur 3,5. En fait, il ne s'est pas complètement
cassé mais avait légèrement plié (plusieurs couches de
carbone se sont sans doute cassées sur un côté mais il tenait
encore très bien.
En fait, contrairement au MP6,
le renfort AV du MP 7,5 est beaucoup plus proéminent et
fortement exposé aux chocs, contrairement à celui AR qui est
protégé par l'aileron. Maintenant, je l'ai passé en épaisseur
4,2 mm ... on verra bien !
Depuis, nous avons participé
à plusieurs courses (Marmousets, Paray et Sens) et nous n'avons
rien cassé ni plié !
|
Cas particulier des
renforts
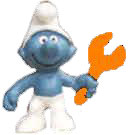 |
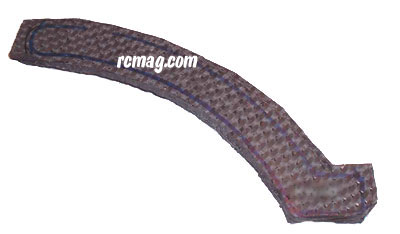 |
En fait, pour ces
pièces, il m'a fallu beaucoup plus de travail car je ne suis pas
parti d'une pièce existante à copier.
J'ai tout d'abord
schtroumpfé un gabarit en carton. Ensuite, j'ai schtroumpfé
deux pièces identiques dans la plaque de carbone de 3,5 mm (phase
1). Ensuite, je les ai schtroumpfées ensemble avec de la cyano
et schtroumpfées fortement dans un étau. On schtroumpfe à ça.
|
Après, il faut
schtroumpfer comme
dans les phases 3 et 4. Ensuite, il faut schtroumpfer en sorte de
stroumfer un pied bien plan qui schtroumpfe après de référence.
Puis, quand c'est schtroumpfé, je schtroumpfe des trous que je
schtroumpfe à 3 avec un taraud. Dans ces trous, je schtroumpfe
des vis chc (vis six pans creux sans tête). Ces vis
schtroumpfent les deux plaques de se schtroumpfer en
schtroumpfant. Il faut schtroumpfer ces vis judicieusement à
proximité des vis de fixation sur le châssis. On ne les
schtroumpfe pas car elles sont schtroumpfées de poussière de
carbone schtroumpfée à la cyano. On n'y schtroumpfe que du feu
!
Ensuite, on
schtroumpfe aux phases 2, puis 5 et enfin 6.
|
Autre réalisation |
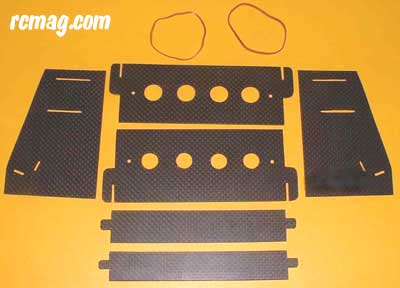 |
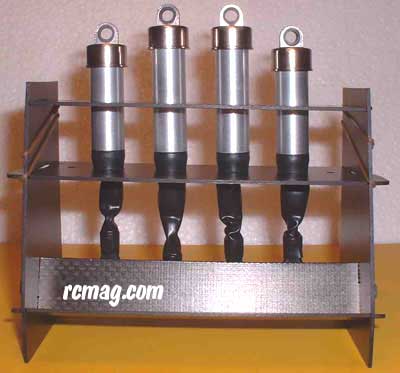 |
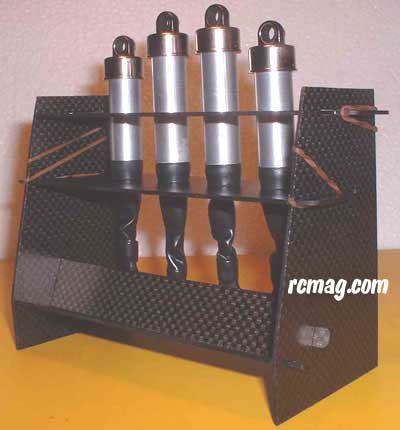 |
Pour le fun, mon fils ayant
vu au Masters le banc de remplissage des amortisseurs de YUCHI
KANAI, il m'a demandé d'en faire un en carbone. Le voici. Il est
entièrement démontable et tient avec deux élastiques qui
assurent la tension et le blocage des pièces. Les plaques sont
en 2 mm d'épaisseur. Le carbone n'est pas aussi pur et aussi
solide que pour les pièces de la voiture. C'est plutôt de l'époxy
avec deux couches de carbone sur chaque face. Préalablement, il
a fallu dessiner le plan des pièces pour qu'elles s'emboîtent
parfaitement et que l'ensemble soit montable et donc aussi démontable
pour tenir moins de place dans les caisses. |
PRECAUTIONS A PRENDRE
A priori
tout semble simple mais ce n'est pas si évident que ça pour celui qui n'est pas
trop habile. A vous de voir. Par contre, il ne faut pas oublier de prendre
quelques précautions en matière de sécurité du travail. La vie coûte plus chère
que les pièces de carbone !
1 - pendant toutes les opérations, il
faut aspirer en permanence les poussières de carbone notamment
lors des meulages avec la disqueuse. En effet les particules de
carbone sont très très fines et partent en nuage. Un bon
aspirateur tenu par une tierce personne fait très bien l'affaire.
Même si le corps humain est fait d'environ 15 Kg de carbone en
moyenne sous différentes formes, ce n'est pas une raison pour
l'absorber par les poumons !
2 - On peut rajouter un
masque anti-poussière
3 - Eviter aussi de mettre ses yeux trop
près du disque abrasif et porter des lunettes de meulage. Même
si le disque est incassable, il vaut mieux être prudent,
4 - Pour la cyano, attention aux doigts
(ça colle bien),
5
- éviter de passer le doigt sur la tranche des plaques juste après usinage. Dans
certains cas, des échardes partent et je peux dire que c'est très difficile
de les enlever (j'ai cotisé !).
|
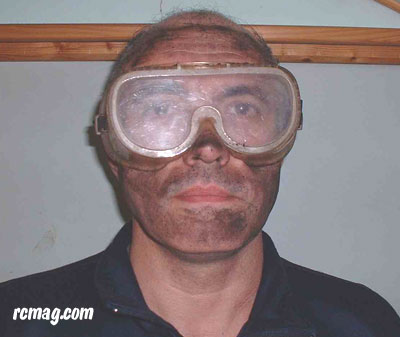 |
Attention à la
poussière de carbone. !!!
Bon là, je
déconne un tantinet. Mais c'est ce qui peut arriver si on n'aspire pas !
sans parler de la propreté de l'atelier ... |
Conclusion
Vous voyez les résultats
obtenus. Vous pouvez aussi l'observer sur la voiture à la
rubrique champion sur ce site. Je pense que le résultat est très
bien et quel plaisir de faire soi-même. Bien entendu,
actuellement, il existe des pièces carbone dans le commerce mais
pas les renforts, na !
La méthode décrite
fonctionne parfaitement avec les pièces planes. Par contre, pour
les pièces courbes, genre les bavettes, il faut avoir les pièces
thermoformées et là, il faut des outils adaptés et ça dépasse
amplement le bricoleur de base.
Je pense avoir avec cet
article montré que c'était quand même accessible à un bon
bricoleur. Je pense aussi avoir démystifié le sujet et que
maintenant on ne verra plus dans les forums certain dire que
c'est très difficile, que c'est dur comme du béton, que les forêts
s'usent vite, que ... De toutes façons tous les outils s'usent
et tous ceux que j'ai utilisés ne coûtent pas la "peau des
fesses" ! ! mais en plus, ils ne s'usent pas plus qu'en
travaillant de l'alu. Ah oui, au fait je fais aussi des pièces
en alu avec pratiquement la même méthode ! Mais c'est la scie
à métaux et les mains comme moteur qui remplacent la disqueuse.
En fait, le plus difficile
est de trouver la matière première (plaque de carbone) à un
prix abordable.
|
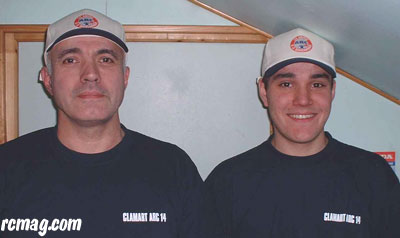 |
Les
bricoleurs
(Tartempion père et
fils)
Voici donc le binôme
Coté face ... |
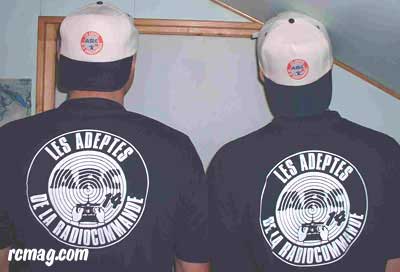 |
Coté pile ...
Vous remarquerez
notre appartenance à
ARC 14. Mon fils "pilote" et moi,
licencié "ramasseur de voitures". Merci au président
du club Nicolas Lazareff qui cette année, avec le prix de la
licence, a offert aux adhérents un tee-shirt et une casquette au
logo du club ! |
Comme je suis en train de
terminer mon article en regardant la remise des victoires de la
musique à la télé, je vais remercier les plaques de carbone
pour leur "tendresse",
Black et Decker et disque
epoxy pour leur efficacité.
Mon épouse remercie
l'aspirateur.
Et
nous on remercie Tartempion !

Vous pouvez retrouver
Tartempion sur le
Kforum
et la voiture du Team rubrique Champions de
Kweb |
Texte et photos de
Tartempion / Mise en page Tractoricou |
Kweb sur
Kyosho.fr |